A Banking Model
The MESPAS platform was developed based on the internet banking model for storing and managing global product data centrally. Banking clients must have instant access to their accounts, data must be consistent around the world, and it must be secure. That is why the data is controlled centrally.
Likewise, for ship management, it is much better to have products, part catalogues, maintenance settings and documents stored centrally and just link them with ships and global offices. The same products are typically installed on hundreds or even thousands of ships, but the data is managed securely and stored centrally in one place. It can only be seen by relevant clients.
This concept reduces the effort required to manage data within a company, because there is only ever one unique dataset. It facilitates reporting and analysis and minimizes the risk of ordering errors.
Plug and Play
All core data is initially loaded on a plug and play server that is directly sent to the ship and installed by the crew. After this, only new information is synchronized, resulting in an average sync file size of a few kilobytes. New software versions are sent via the same process and installed automatically on board.
Maintenance and Optimization
The management of machinery maintenance can be linked to the database, with functionality to support planned maintenance – including task management. The system can be connected to a ship’s automation system which records running hours and sensor data, resulting in more accurate analysis and less manual data entry for the crew. Both equipment monitoring and rationalization of maintenance schedules are possible. Also included is a reporting system that provides managers with real-time KPIs for their ships and dashboards giving an overview of fleet performance.
The maintenance module is connected to the procurement function and stock levels in order to record the consumption of parts. Reporting of the cost per overhaul and forecasts for upcoming maintenance can be managed with the click of a button.
Global Operations
The MESPAS platform is already used by over 21,000 maritime suppliers, trading over $600 million a year globally. Ship managers using the system span the wet and dry bulk and container trades. In addition to procurement and maintenance, MESPAS functionality includes:
- QHSE: task management, inspection reports, document and form management, reporting engine, analytics and dashboards.
- Operations: noon report, ship schedule, voyage analytics and installation data management.
- Crewing: crew management, work and rest hours, automated payroll, travel and training.
Source: The Maritime Executive
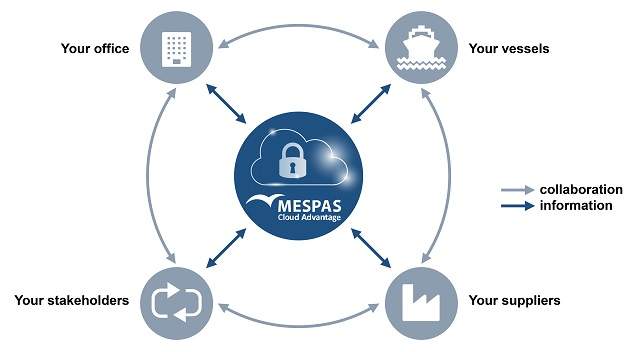
A cloud-based database containing the details of millions of machinery parts has eliminated inventory inconsistencies for technical managers – now it is also being used to support procurement contracts.
The MESPAS global master database is a unique maritime software solution. It includes every part and component needed for shipboard equipment including engines, pumps, navigation equipment and much more. The MESPAS functionality means all vessels in a fleet are supported by one dataset to enable purchasing economies of scale and reduce data entry effort. Unlike other systems, the MESPAS method ensures complete data consistency, and no manual data entry is required.
MESPAS procurement functionality already covers inventory administration, budgeting and invoice management. Now, it has been expanded to reduce the amount of administrative work involved in creating procurement contracts. The first stage of the development is the Auto Quoter that automatically creates quotations for suppliers based on the price lists they have defined in the system. Offers can be sent out in a matter of seconds. The system is expected to result in a 90 percent time saving for suppliers and a 60 percent saving for ship managers.